Plant Manager
Terrell, TX, US
Engineering
Bachelors Degree
Full Time, Direct Hire
Manager (Manager/Supervisor)
On-site
Manufacturing - Other
First Shift (Day)
Terrell, TX, US
Manager (Manager/Supervisor)
Full Time, Direct Hire
Manufacturing - Other
On-site
Engineering
Bachelors Degree
First Shift (Day)
Job details
Plant Manager (Terrell, Texas)
Our client located in Terrell, Texas, is currently hiring a Plant Manager, relocation assistance may be provided. This is a new role, created due to growth, that will be the head person at growing facility when Regional Plant Manager is not present.
Client provides a broad range of solutions to meet specific waterproofing needs, this includes technical services, research & development and manufacturing capabilities from several locations. They offer a complete line of waterproofing and moisture protection products for the architectural, general construction, industrial and maintenance industries.
First 90 days of this role will focus on safety, learning production, then finally, reporting. Long-term goals of this role are safety, lean sustainability, managing staff, and leading new projects (infrastructure/ construction, machinery, etc.). Plant Managers, Regional Plant Managers who no longer wish to travel, Project Managers with an Engineering background (Mechanical, Manufacturing, Industrial, Chemical), or Industrial People Supervisors, all may do well in this role.
The Plant Manager has general management responsibility for the overall manufacturing processes as well as the physical facility. This includes accountabilities for all products manufactured, all aspects of safety performance including environmental, product quality and quantity, personnel hiring and discipline, training, budgeting, shipping & receiving, cost control and reduction, and development of a strong team environment with clear and effective communications. The Plant Manager serves as the key interface with a variety of support personnel including R&D, Engineering, Technical Services, Scheduling, Sales, Customer Service and Logistics. This position will utilize the Carlisle Operating System framework as the foundation for the training of employees and to support operational requirements. Scope of the job hours of operations is 7 a.m. to 5 p.m., Monday through Friday with “on call” 24-hour availability. Possible weekend hours may be required to meet production demands in busy season. Occasional travel to other facilities for meetings or training; typically no more than 15% travel.
More about this location –
The plant runs two shifts, working four days a week, ten hours a day, with Fridays and Saturdays being used for overtime. The first shift starts at 7 am. There are approximately 60 employees on-site, and this position will have five to six direct reports. The biggest challenge for this plant is the installation of automation, so the candidate must have strong experience in change management and continuous improvement. This plant is so busy a Maintenance Manager has also been hired to delegate work. This person will be starting in May, team would love to have the Plant Manager start around the same time.
Duties and Responsibilities:
Site Development- Develop a manufacturing team to provide exceptional customer service at the lowest possible cost while maintaining a safe work environment. Specific duties include management of employee development/training, plant scheduling, recruiting/terminations, customer contact, financial tracking, safety implementation, supplier evaluation, and process improvement.
*Create an environment for success among supervisory and production employees. It is pertinent that the Plant Manager convey an attitude that is positive and confident. He/she must direct the staff to
achieve their highest level of performance while treating them with respect and dignity.
*Coach and develop supervisors and team leaders in their managerial skills to align with overall company goals.
*Work with purchasing, environmental, health & safety, engineering, human resources, and corporate staff. The Plant Manager will be called upon to be the local expert for their plant regarding these topics.
*Manage the buildings and grounds to ensure good manufacturing practices are adhered to and a professional appearance is maintained.
*Continuously monitor compliance with all environmental permits pertaining to the manufacturing process and facility.
Oversight and leadership of the Lean Manufacturing journey in the plant- This includes leveraging the Carlisle Operating System (COS) to drive daily, incremental improvement in all aspects of the site. Additionally, strong emphasis on employee engagement, capacity improvement, visual management, and advanced manufacturing techniques are required for success in this role. The Plant Manager is expected to be the “champion” of the COS implementation.
Inventory Control – This involves releasing all raw materials, supplies and finished goods. The Plant Manager is also responsible for implementation of an inventory audit procedure to ensure accurate inventories are always maintained.
Required Knowledge/Skills/Abilities:
Bachelor’s degree engineering, business administration or related field preferred.
10+ years of experience in a manufacturing position or plant operations.
Strong experience in change management and continuous improvement.
Prior experience in operations research/process flow and scheduling.
Prior experience with Lean Manufacturing and 5s.
Understand fundamentals of coaching, counseling, and feedback.
Strong problem analysis and resolution skills.
Comprehension/understanding of reading, speaking, and math skills.
Ability to measure performance of standards and goals.
Efficient problem-solving skills and ability to work in stressful work situations.
ISO9001/14001 experience a plus.
Knowledge of manufacturing processes and products as well as quality systems and associated literacy of SPC, SOP’s, process specifications, etc.
Knowledge of government regulations as they relate to people, plant, and process operations such as FMLA, OSHA, FLSA, ADA, Workers’ Compensation, EPA and unemployment.
Lean Manufacturing and Six Sigma methodologies.
Financial and accounting familiarity including budgeting, cost control, financial data, project justification, and ACE process.
Overall understanding of the logistics process including raw material and finished goods shipments and customer service.
Strong knowledge and experience with MS Office Suite.
Strong knowledge and experience working in an ERP system, preferably SAP.
Strong oral and written communication skills including the ability to speak in front of groups and make effective presentations.
Good organizational skills along with effective time management.
Ability to effectively delegate to subordinates and others in supporting roles.
Excellent problem-solving skills and the ability to handle stress and make decisions under a variety of challenging circumstances.
9224501
I want more jobs like this in my inbox.
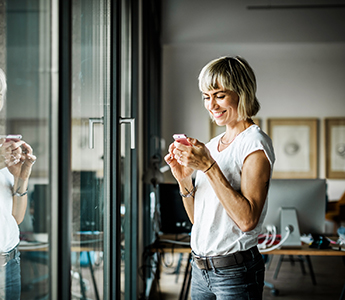
Why Kelly®?
As a worker today, it’s up to you to take charge of your career and look for opportunities to learn, grow, and achieve your potential. Helping you find what’s next is what we’re all about. We know what’s going on in the evolving world of work—just ask the 440,000 people we employ each year. Connecting with us means getting the support, guidance, and opportunities needed to take your career where you may have never imagined.About Kelly
Work changes everything. And at Kelly, we’re obsessed with where it can take you. To us, it’s about more than simply accepting your next job opportunity. It’s the fuel that powers every next step of your life. It’s the ripple effect that changes and improves everything for your family, your community, and the world. Which is why, here at Kelly, we are dedicated to providing you with limitless opportunities to enrich your life—just ask the 300,000 people we employ each year.Kelly Services is proud to be an Equal Employment Opportunity and Affirmative Action employer. We welcome, value, and embrace diversity at all levels and are committed to building a team that is inclusive of a variety of backgrounds, communities, perspectives, and abilities. At Kelly, we believe that the more inclusive we are, the better services we can provide. Requests for accommodation related to our application process can be directed to Kelly’s Human Resource Knowledge Center. Kelly complies with the requirements of California’s state and local Fair Chance laws. A conviction does not automatically bar individuals from employment.